What Spare Parts Do You Need To Maintain A Pipe Threading Machine
What spare parts do you need to maintain a pipe threading machine?
For a heavy duty made in China pipe threading machine usually we offer one year warranty, while for a economic type pipe threader we offer 3 month warranty. After this period you will have to buy extra replacement parts to fix the machine.
First of all, the threading dies(chaser) and cutting blade are wearing parts, regardless of wether the quality of machine is good or not you will have to prepare them. Normally a threading dies life span is hundreds of pipes, the life of the die depends on the material 9Cr2/9CrSi/HSS and production craft.
Secondly, if you are an end user who purchased a pipe threading machine for your own use, buy a complete assembly parts will be easier for you to change old one. For example, you can buy a complete die head, a complete pipe cutter, pipe reamer, front chuck set, rear chuck set, motor, gear box, oil pump. This will solve 90% problem.
However, if you would like to replace a single parts, you can refer to below chart (Chart No.1), this is an explosive view of all the parts on a pipe threading machine.
Chart No.1
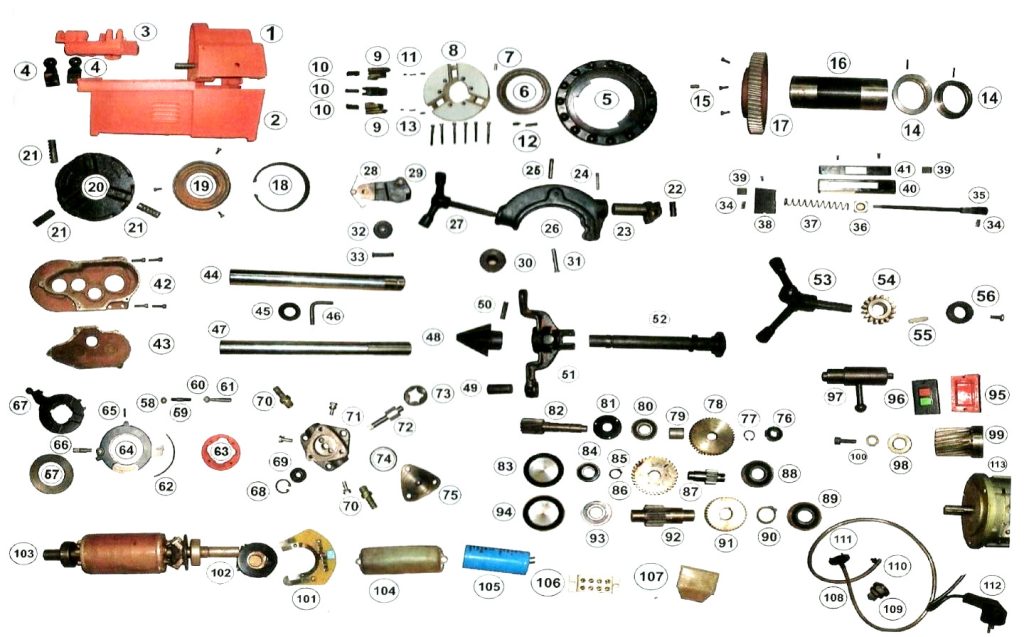
Here is a general concept what kind of replacement parts will you need in maintaining a electric pipe threader (showing what our client buy regularly), client is a professional tools wholesaler with his own engineer for pipe threading machine maintainence.
Description of goods | Quantity |
SETS | |
SPARE PARTS OF PIPE THREADER | |
2″ Machine Automatic Die Head | 75 |
3” Machine 1/2”-2” Automatic Die Head | 30 |
3” Machine 2.1/2”-3” Automatic Die Head | 10 |
4” Machine 1/2”-2” Automatic Die Head | 30 |
4” Machine 2.1/2”-4” Automatic Die Head | 10 |
2” Machine 2” Die Head Curve Plate | 50 |
4” Machine 2” Die Head Curve Plate | 50 |
1”-2” BSPT 9CRSİ Dies | 100 |
1/2”-3/4” BSPT 9CRSi Dies | 50 |
2.1/2”-3” BSPT 9CRSİ Dies | 30 |
2.1/2”-4” BSPT 9CRSİ Dies | 30 |
1”-2” BSPT Alloy Dies | 100 |
1/2”-3/4” BSPT Alloy Dies | 50 |
2” Machine Pipe Cutter Assembly | 50 |
3” Machine Pipe Cutter Assembly | 10 |
Pipe Cutting Blade | 300 |
2” Machine Hammer Chuck Complete Set | 15 |
3” Machine Hammer Chuck Complete Set | 5 |
4” Machine Hammer Chuck Complete Set | 5 |
2” Machine Hammer Chuck Screw Plate | 50 |
2” Machine Jaw Teeth (3pcs set) | 100 |
2” Machine Jaw Body (3pcs set) | 20 |
3” Machine Hammer Chuck Plate | 5 |
4” Machine Hammer Chuck Plate | 5 |
3” Machine Rear Chuck Plate | 5 |
4” Machine Rear Chuck Plate | 5 |
3” Machine Rear Chuck Jaw | 10 |
4” Machine Rear Chuck Jaw | 10 |
2” Machine Big Gear And Main Cylinder Shaft | 30 |
3” Machine Big Gear And Main Cylinder Shaft | 3 |
4” Machine Big Gear And Main Cylinder Shaft | 3 |
2” Machine Main Shaft Sleeve | 20 |
3” Machine Main Shaft Sleeve | 5 |
4” Machine Main Shaft Sleeve | 5 |
2” Machine Lever Arm | 30 |
2” Machine Distance Adjusting Complete Unit | 50 |
3” Machine Distance Adjusting Complete Unit | 10 |
4” Machine Distance Adjusting Complete Unit | 10 |
At this moment, the most frequently used parts are as below.
FREQUENTLY REQUIRED
Dies and die head, die head curve plate, big gear and main shaft, motor, oil pump, front chuck jaw teeth and jaw body, switch.
SOMETIMES NEEDED
Front chuck and rear chuck, rail rod, distance adjusting unit, pipe cutter blade, scroll plate and sleeve.
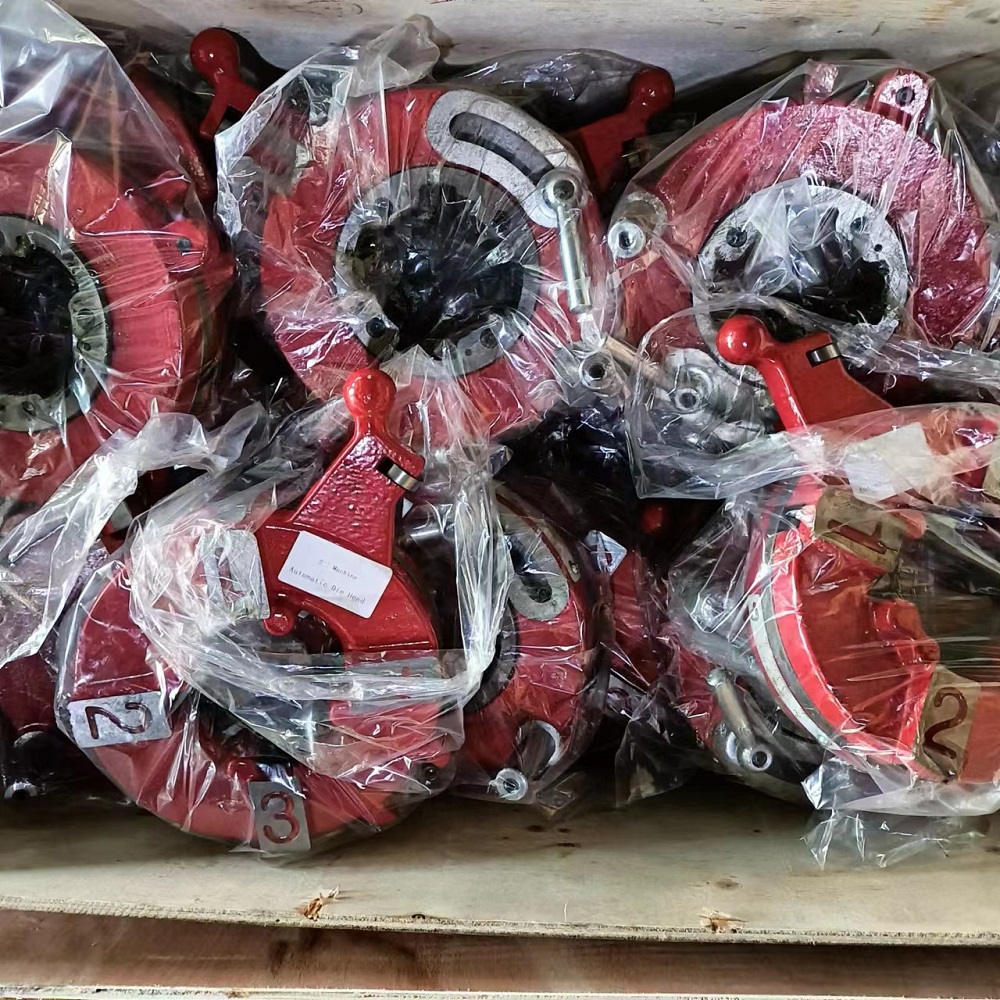
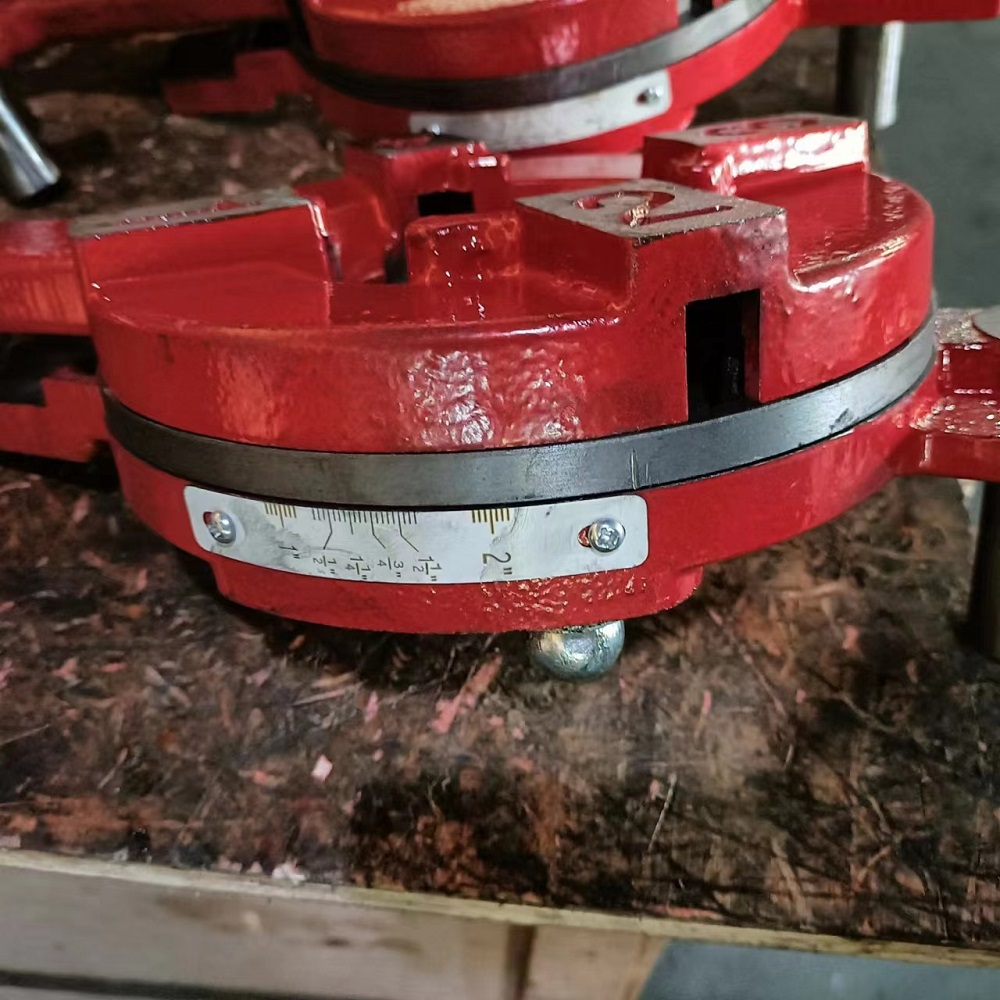
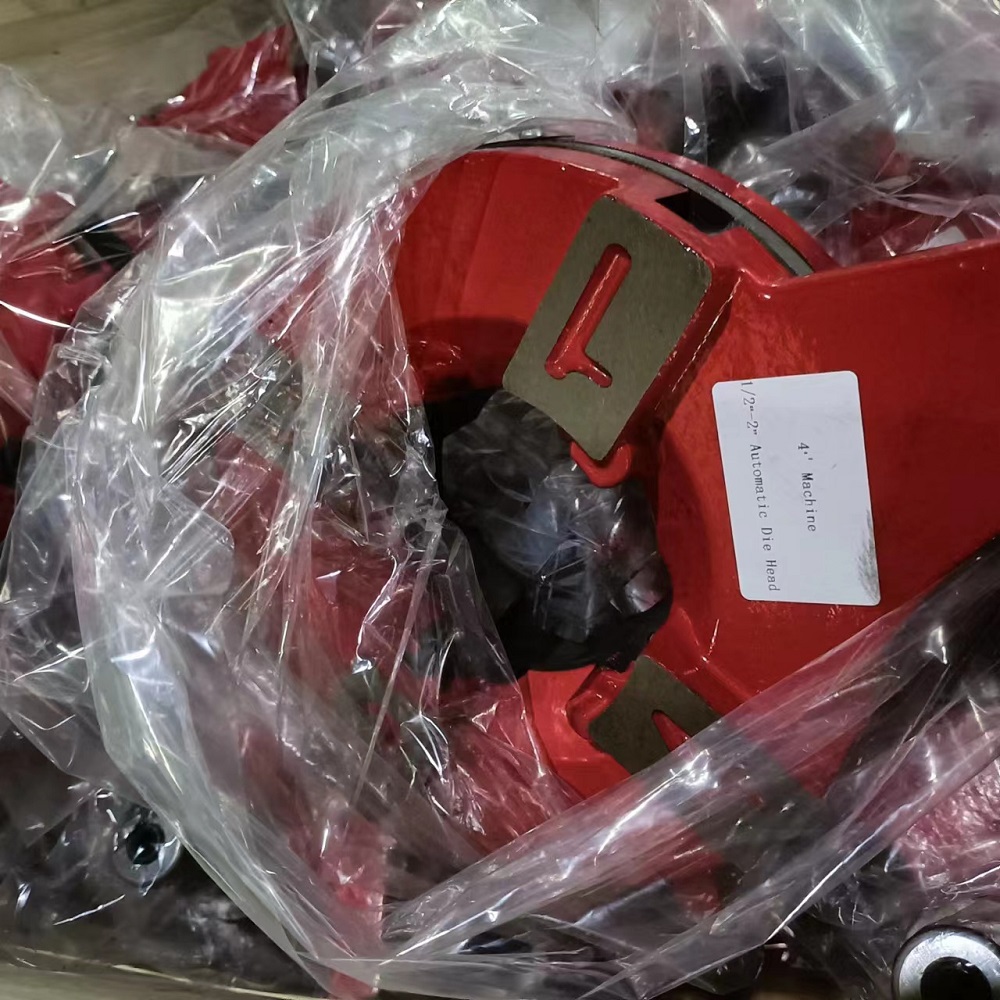
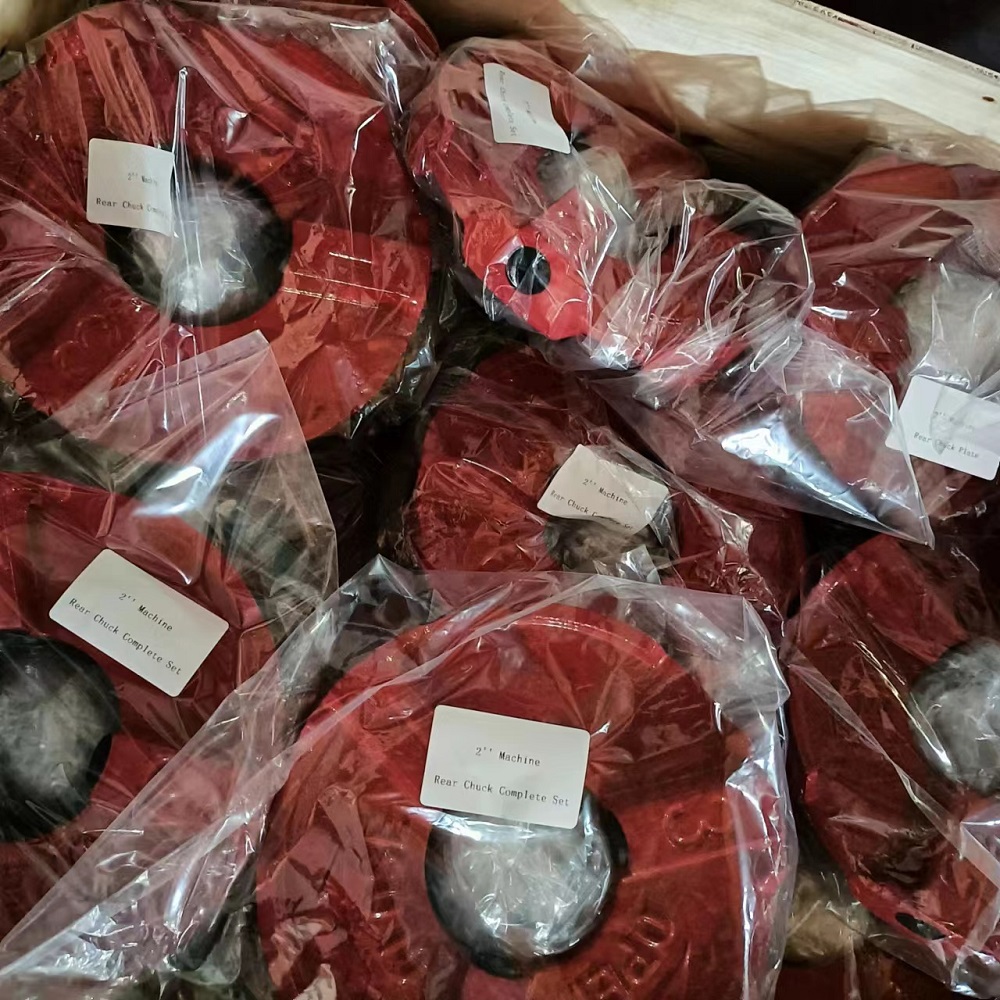
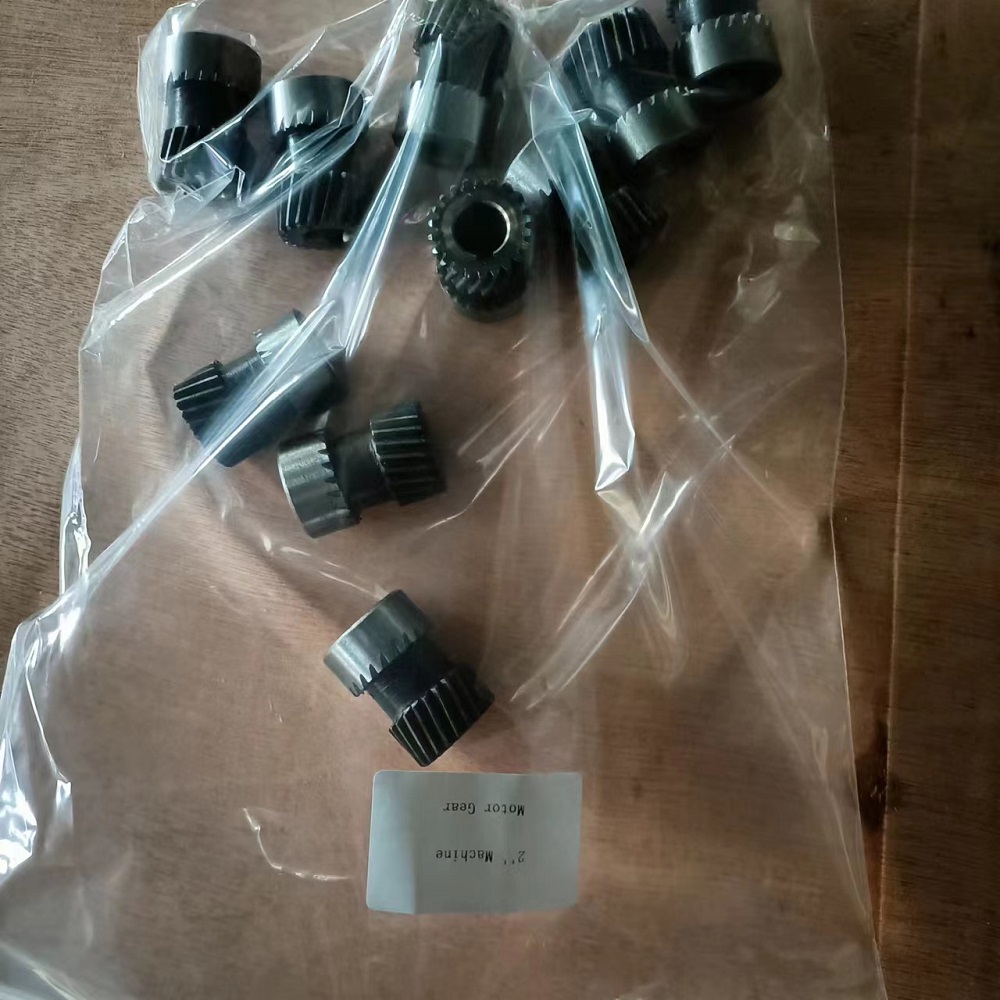
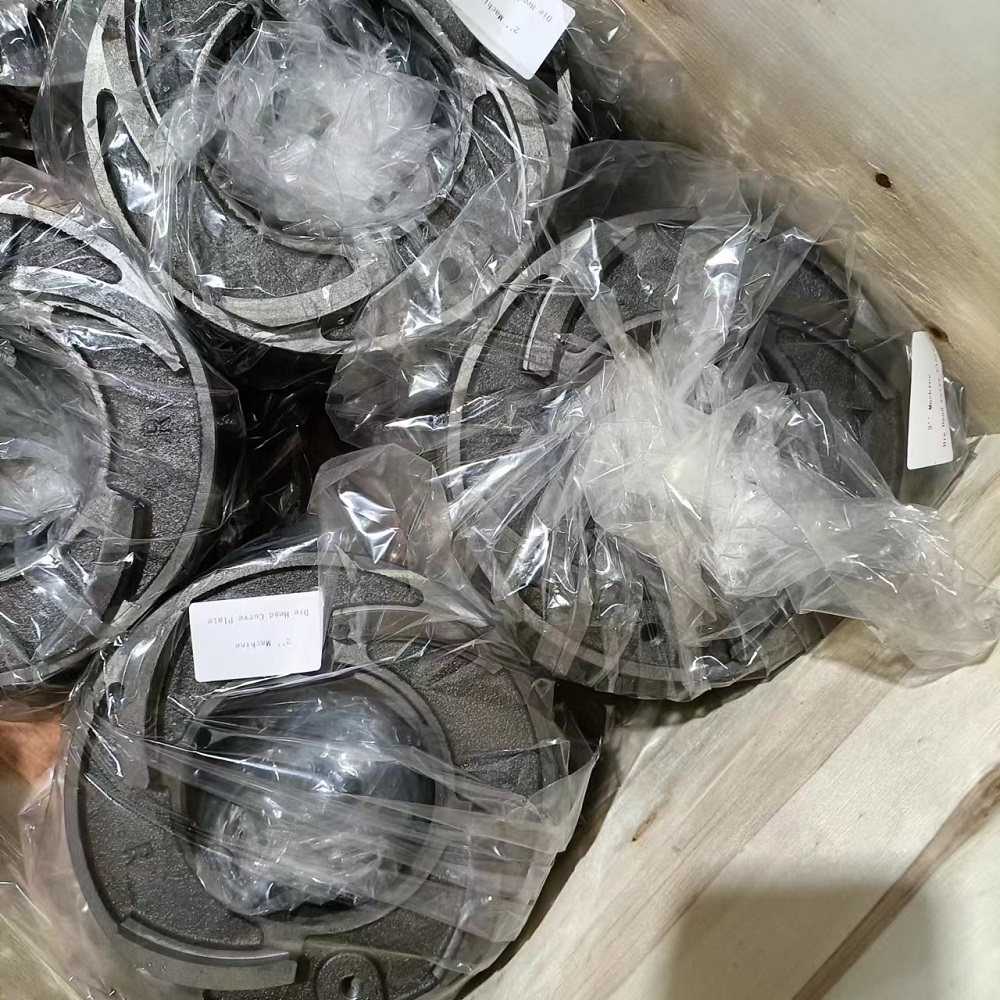
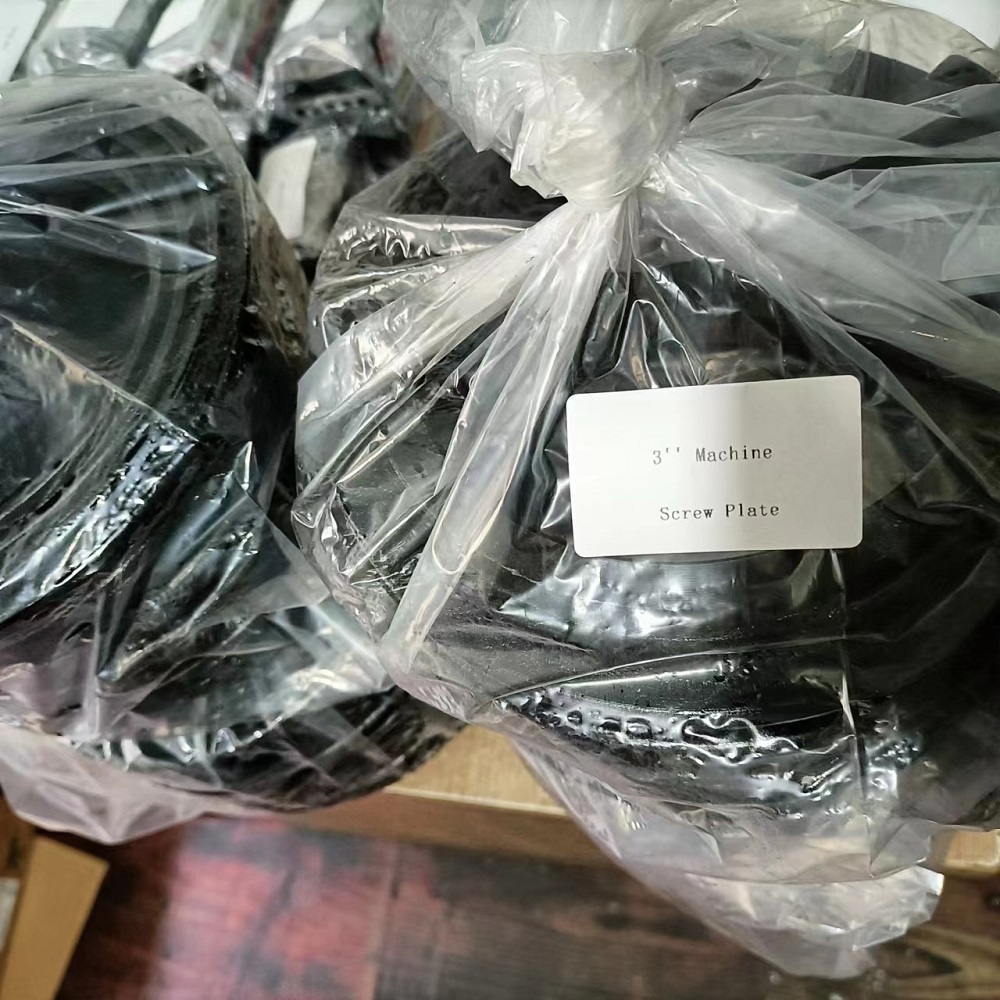
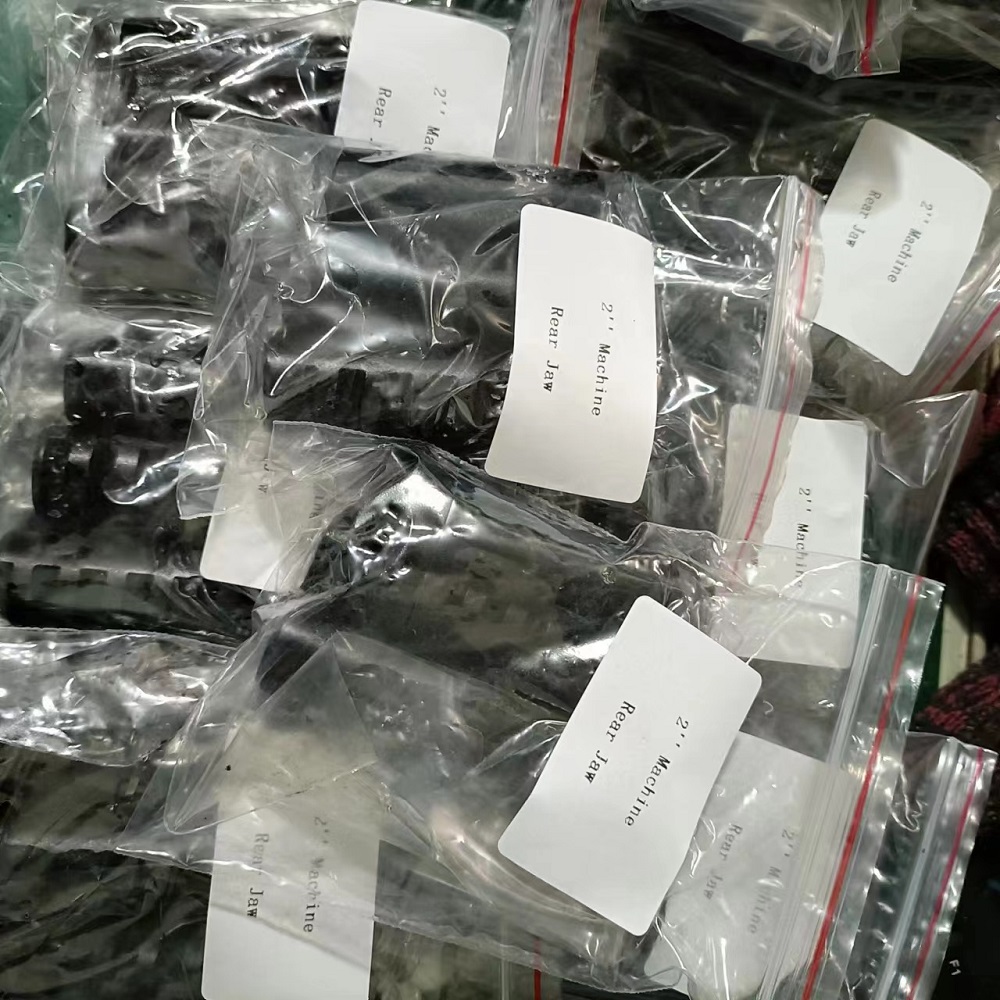
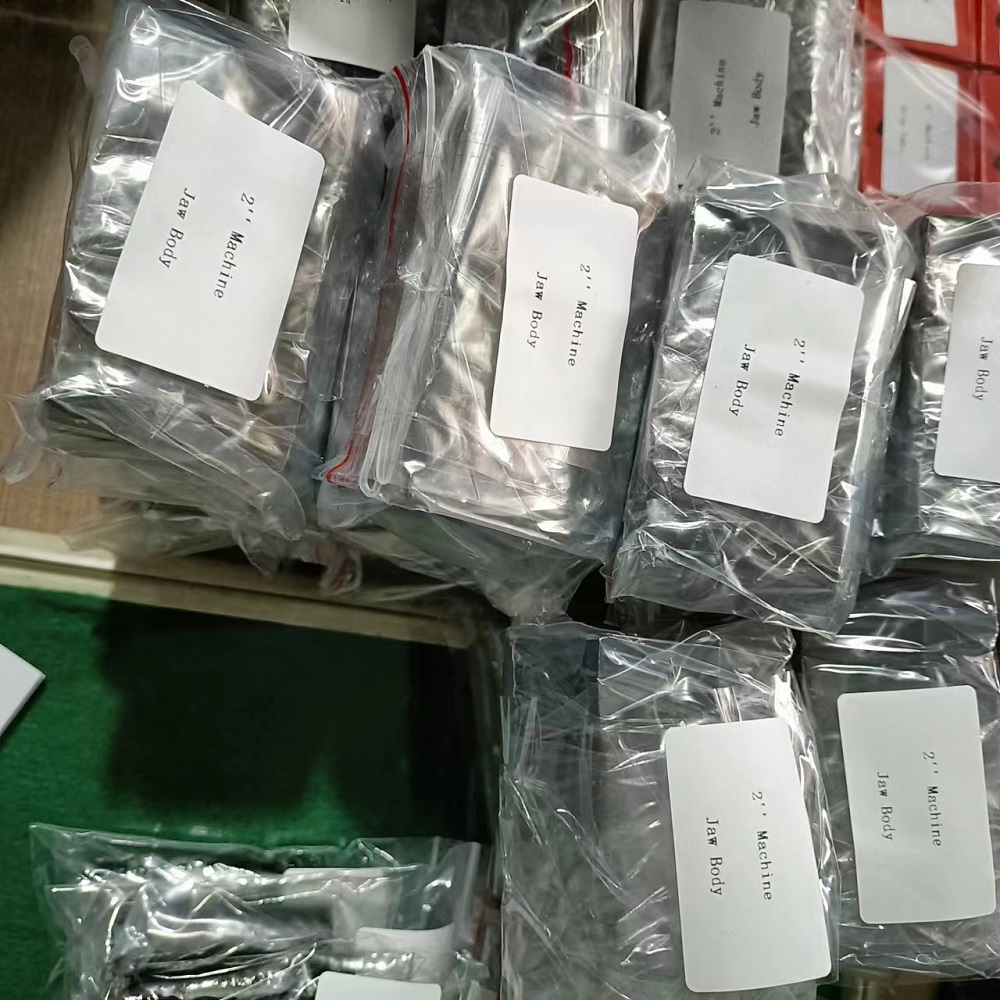
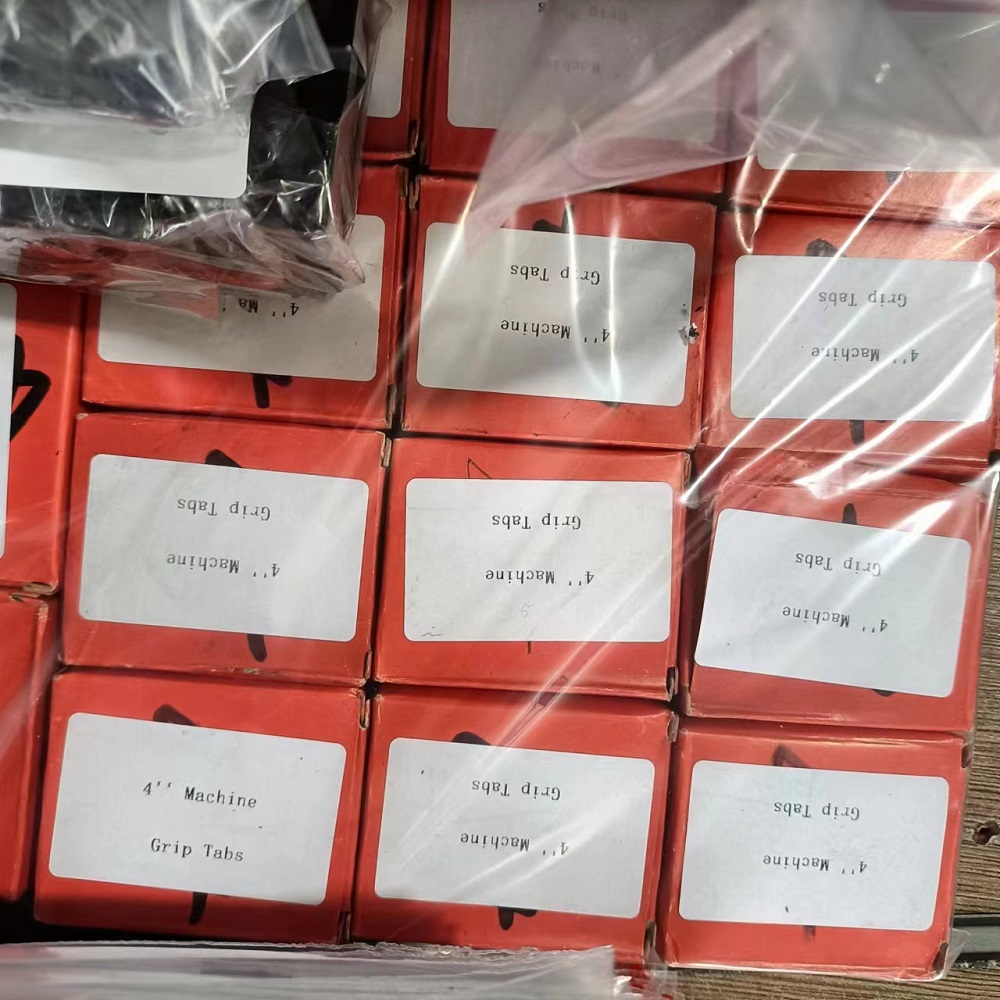
Maintenance of electric pipe threading machine
- Threading dies
When one threading die is damaged, the other three threading dies shall be replaced at the same time, in order not to affect threading quality.
- Cutting and chamfering
If the handle of cutting knife is rotated too violently, when cutting knife is cut into the pipe, the pipe may be deformed, cutting knife wheel may be broken and cutting knife seat may be cracked.
- Cooling lubricating system:
(1) Ensure sufficient oil in oil tank, and all pipelines are smooth.
(2) If oil turns colors or becomes dirty, clean the oil tank and use new oil.
(3) Clean oil filtering tray and oil absorption filtering tray after using for 8 -12 hours.
(4) Since small scrap iron is mixed into the oil tank during threading, to ensure normal operation of threading machine, it is crucial to clean oil filtering tray regularly.
(5) This machine adopts special oil of threading machine as cooling lubricant.
- Cutting knife:
(1) If cutting knife wheel becomes blunt or damaged, replace it.
(2) Timely clean and apply oil to feeding screw and roller of cutting knife.
(3) Inspect the wear and tear of cutting knife, pin roll of roller and pin roll of cutting knife.
(4) Clean and lubricate cutting knife blade and pin roll. Cutting knife wheel shall be lubricated with viscous heat-resisting oil.
- Replacement of clamping jaw tip:
(1) Take out inner hexagon screw with internal hexagonal wrench.
(2) Take out spring and spring seat.
(3) Take out clamping jaw tip.
Installation of clamping jaw tip:
(1) Put a new clamping jaw tip in place.
(2) Put in jack-prop and spring.
(3) Install screw, until it cannot rotate.
Trouble Shooting | ||
Common faults | Reasons | Solutions |
1. Motor doesn’t work or work with intermittent sound | 1. Fuse is burnt down | 1. Detect the broken part with a multimeter and use a new fuse |
2. The plug is not well connected | 2. Replace the plug or socket | |
3. The internal part of the cable is broken | 3. Replace the power cord | |
4. The button switch is not well connected | 4. Replace the switch | |
5. 100UF Capacitor breakdown | 5. Use a new capacitor | |
6. Environment temperature is too low, and lubricating grease solidifies. | 6. Operate indoor or help it to start up | |
2. Pipe fails to be fixed and slips during threading | 1. Insufficient hammering force | 1. Hammer hard |
2. Clamping jaw teeth turns over | 2. Adjust clamping jaw tip | |
3. One clamping jaw teeth breaks or has a gap | 3. Use a new clamping jaw tip | |
3. Cutting knife fails to cut | 1. Sharp corner of cutting knife is worn out and becomes an arc | 1. Replace cutting knife blade |
2. Pin roll of cutting knife is worn out | 2. Replace pin roll | |
3. Cutting force is insufficient | 3. Cut more vigorously | |
4. Threading dies cannot cut thread | 1. Opening of threading die is too small at the start of threading | 1. Ensure the opening distance fit the pipe diameter |
2. Several teeth of die are broken | 2. Replace the die | |
3. Knife head doesn’t match | 3. Re-install knife head | |
4. There is scrap iron in die groove | 4. Clean threading die head | |
5. Front chuck loosens and falls down | Screws loosen due to long-term use | Inspect them timely |
6. Main shaft is heated and jammed | Insufficient oil | 1. Add oil timely |
2. Exit beam barrel and repair shaft sleeve | ||
7. Cooling oil doesn’t come up | 1. Oil line is jammed | 1. Clean oil line |
2. Oil hole doesn’t align after dismantling and re-assembling fulcrum shaft of die head. | 2. Re-assemble | |
3. Oil leaks from oil pump after stopping use for a long time | 3. Add some cooling oil into oil pump | |
4. Oil pump is worn out | 4. Replace oil pump | |
5. Rotor pin roll of oil pump is broken | ||
8. Oil leakage | 1. Oil line plugging leads to falloff or rupture of oil line. | 1. Inspect plugging point and replace oil line |
2. Oil draining screw in the oil tank isn’t tightened | 2. Tighten oil draining screw | |
9. Cooling oil leaks into motor | Skeleton type oil seal of oil pump PD8×22×8 is damaged | Replace a new oil seal or oil pump |
10. Three-phase motor is burnt down | Phase loss or bad contact | Carry out the winding and check the circuit |
11. Single-phase motor is burnt down | 1. Starting voltage is too low | 1. Wind wires and inspect voltage; replace qualified power line and power supply |
2. Environment temperature is too low, and lubricating grease solidifies. | 2. Wind wires and carry out indoor operation | |
12. Unilateral threads | 1. Oval pipe | 1. Replace the pipe |
2. Clamping jaw teeth breaks or has a gap | 2. Replace the clamping jaw teeth |